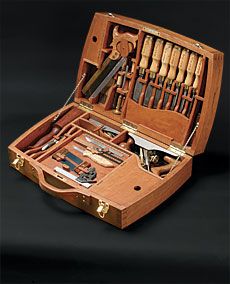
Sharp edges in wood carving tools enhance your pleasure of carving. These are some common methods for sharpening wood carving tools. Sharper edges will also last longer than duller ones and are therefore more durable. Sharp edges allow for more efficient use of your tools. Sharp edges facilitate carving and maximize cutting performance. The following are three common ways of sharpening wood carving tool. Continue reading to learn more. - Sharpening a stone.
Sharp edges are a great way to enhance your carving experience
Sharp tools will not only make carving easier, but sharp edges are essential. Sharp tools are easier to use and allow for more control when carving. A smooth, well-cut blade gives you a smooth cut. A successful carving project requires sharp tools. Sharpen your tools often to achieve the best results. Regular sharpening will keep the tools sharp and makes carving easier.
Sharp edges may enhance the enjoyment of carving, but can cause blisters. Wood's natural texture, which is rough, will be toughened by regular handling. Although blisters will eventually turn into calluses, this can be painful and time-consuming. If you notice blisters in your carving, try to change the way you hold your tools. It may take some practice, but the effort will be well worth it.
When sharpening your knives, begin by using a sharpening kit and a fine-grained stone. Check for any damage to the edge. Chips near the edge require more aggressive grinding. An edge that is dull may need minimal grinding with a finer grinder. The knife can be tested by cutting through some paper or rope. You don't need to use a sharpening knife if your knife has been dull for a while.
Common techniques for sharpening wood carving tool
There are many options for sharpening wood carving instruments. There are oil stones, water stones, ceramic stones, and diamond sharpening stones. Oil stones need oil to be applied to the stone's surface in order to prevent metal particles embedding into the surface. The best stones for sharpening carbide tools are ceramic and diamond. They don't need oil. This article will cover the most common methods of sharpening wood carving instruments.
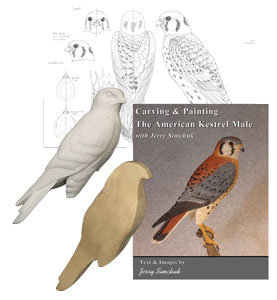
The leather strop is used to remove the wire from a blade's edge and polish it. Although leather strops can be used with all tools, some carvers prefer using a textured one. Flat leather strops are best for straight tools and the edges of gouges. If you are serious about your work, you might consider a leather scrapper with grooves.
Bench chisels have been sharpened traditionally at a 25-degree angle, with a secondary bevel of 5 degrees. Modern alloys are not compatible with these angles and may crack. To correct this, raise the angle of bevel. This will require more force, but you'll have less control. Similarly, block planes are usually sharpened at a 20-degree angle.
A sharpening stone is used
A sharpening knife is a tool that can be used for wood carving. The stone's crystalline form contains grit. This mineral is hardier than steel and has sharp edges. Most stones will need a lubricant in order to cut properly and prevent metal particles from embedding into it. Once you have sharpened your edge to make it easier to cut wood, it will also be less resistant. The strop, usually made of leather, serves to polish the edge and remove the burr.
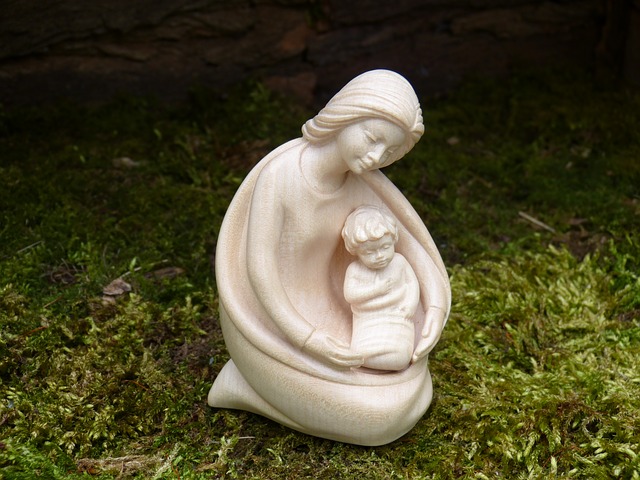
There are many types of sharpening stone on the market. There are oilstones (waterstones), ceramic stones, and others. The oil stones use oil to prevent small metal particles from embedding in the stone. Ceramic and diamond stones do not need any lubricants. They are both effective in sharpening carbide wood carving tools.
The Sentima sharpening stone is a great example of a quality sharpening system. It has both a coarse stone and a fine stone made from corundum. This material features a consistent grain that allows for fast cutting and smooth finishes. Its unique design is easy to clean. The sharpening system is made out of durable materials and will last years without losing quality.
FAQ
How do I get started as a woodworker?
Woodworking is an art form that requires patience and practice. Learning how to use the various tools and techniques necessary for woodworking takes patience.
There are many different types of woodworking equipment available on the market today. Some people prefer to use power tools while others prefer manual tools.
You have the freedom to choose what tool you want, but it is important that you select the right tool for your job. Start with a basic set if you don’t have any previous experience.
You could also try learning how to use a router which is used to cut intricate shapes into wood. You can find these at most hardware stores.
Where do I get my woodworking supplies?
There are many places that you can find all the information you need. You could go to your local hardware shop or visit websites such as Amazon.com.
You can also look for used furniture at flea markets or garage sales.
How can I learn basic woodworking skills
It is an excellent way to learn how to build furniture. You can make a simple bench yourself. This project can be completed with whatever wood you have available at home. If you are unsure what type of wood is best, you can get cheap pine boards at Lowes (or Home Depot) instead. You'll need to sand the bench after it's built. Then, finish it with varnish or a stain.
What would be your first step in woodworking?
Start off with softwood like pine and poplar. These two are the easiest to master, then you can transition to hardwood.
Where do you start when it comes to woodworking?
Building furniture is the best way to learn how furniture is made. You'll need tools, and you'll have to make mistakes along the way, but if you keep at it, you'll eventually figure out what you're doing.
Choose a project that interests you. You can make a simple box or a large entertainment center. Once you have chosen a project, locate a local woodworker who is skilled in this kind of work. Ask him or her for advice on what tools you'll need and where to find them. Perhaps you could ask if there is someone else who does this type of work.
Statistics
- Woodworkers on the lower end of that spectrum, the bottom 10% to be exact, make roughly $24,000 a year, while the top 10% makes $108,000. (zippia.com)
- If your lumber isn't as dry as you would like when you purchase it (over 22% in Glen Huey's opinion…probably over 10-15% in my opinion), then it's a good idea to let it acclimate to your workshop for a couple of weeks. (woodandshop.com)
- The U.S. Bureau of Labor Statistics (BLS) estimates that the number of jobs for woodworkers will decline by 4% between 2019 and 2029. (indeed.com)
- Overall employment of woodworkers is projected to grow 8 percent from 2020 to 2030, about as fast as the average for all occupations. (bls.gov)
External Links
How To
How to make wood joints
This tutorial will help you join two pieces of wooden together. We will use the pocket hole joint, which is drilling holes in the wood to join them. This method works great if your wood is straight and smooth. You might consider dowel joinery if your wood isn’t straight or flat. These are the steps
-
Drill Pocket Hole Joints. First, measure the area where you wish to place the pocket joint. Then drill 3/4 inch deep holes into the ends of each piece of wood using a jig saw or handheld drilling machine.
-
Sand Smooth. Sanding the wood's edges will ensure that the joint doesn't split.
-
Glue Together. Apply glue to both sides of the wood. Allow it to cool for at least 5 minutes before you attach the pieces.
-
Connect the pieces. After the glue has dried completely, you can clamp the pieces together until they are flush.
-
Trim Joinery. After the glue dries completely, trim off any excess wood around the joint.
Allow enough space between pieces so you can turn them inside out.