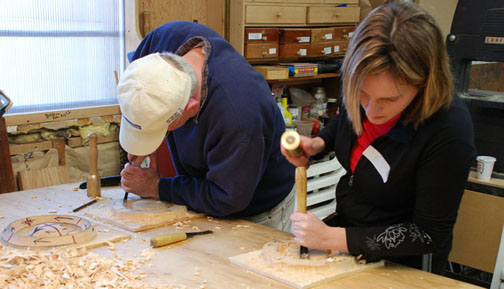
This is the place to learn how to carve wood-carved caricatures. This page will explain the techniques and safety involved in creating wood-carved caricatures. It's possible to make a caricature from a standard image into a masterpiece. You don't have to know where to begin if you aren't sure how to get started. Here are some tips for making your caricature stand out. You can also take classes with caricaturists.
Techniques
Wood carving caricatures is a rare form of sculpture. They're funny and can tell a tale without words. Caricature depicts a cartoonized version of a real person. Dave Stetson and other wood carving carvers adhere to strict rules to ensure realistic results. This article will cover the basics of caricature-carving and give tips for creating one.
First, it requires great focus when carving an astronaut. The two most delicate tools for carving an astronaut are the whittling or spoon knives. To make it easier to work with, templates can be used while you carve the astronaut. Finally, a good tutorial will provide step-by-step instructions on how to finish your caricature. If you're working on a budget, you might want to look into buying a tutorial for this specific subject.
Designs
You can create wood-carved caricatures in many different ways. An excellent way to begin is by using a template. You can also buy a cardboard cutter and use the same patterns to carve different types. You can also use the tutorial to carve a caricature. This article will help you learn about the best techniques and designs for carving a caricature.
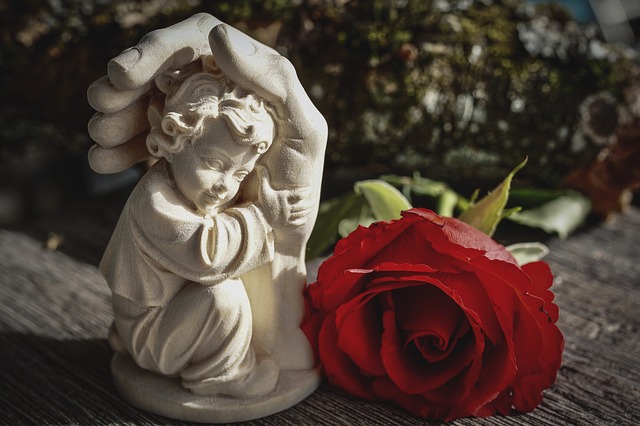
Fred created the first caricature he ever made, called "Aristocrats of the Roads". It showed two men-wanderers. It was made out of Honduras Mahogany. Fred entered it to competitions, and won numerous awards. It was also featured in the Chipping Away Catalog. Fred carved another Luciano Pavarotti caricature, which earned him a Second Place Winner Award at the national woodcarving convention.
Eyes
It is important to ensure realistic looking eyes when carving caricatures. A caricature with realistic eyes is acceptable, but it can be frustrating for the viewer if the detail is not sufficient. Take a picture of an existing carving to ensure that your eyes align properly. Then, follow the steps in the photograph.
Next is to determine the eye shape. Some carvers use the identical eye shape to create their eyes. To create more realistic eyes, others use different shapes. You can make your eyes symmetrical by using stop cuts to cut the lower eyelid. The iris and pupil will also need to be carved. You can now move on to the next stage of carving the caricature.
Safety
Wood carving caricatures are unique in their designs. They can tell a story without words, and the artists that create them take great care to ensure the accuracy of their work. Caricatures are usually depictions that exaggerate people or things to convey an impression. Dave Stetson, a wood carving carver, has set strict guidelines for safety and quality. He also provides information to consumers.
Before carving a caricature, first, clean the wood and remove any pencil marks. You can wash the wood with soapy water or dish soap. For the neck and head carving, you will need a 60-degree V shape tool. An easy-to-use 60-degree V shaped tool can help with the carving process. A good choice for this type of tool is the Ramelson 60-degree V-shaped carving tool, as it is sharp and easy to use.
Materials
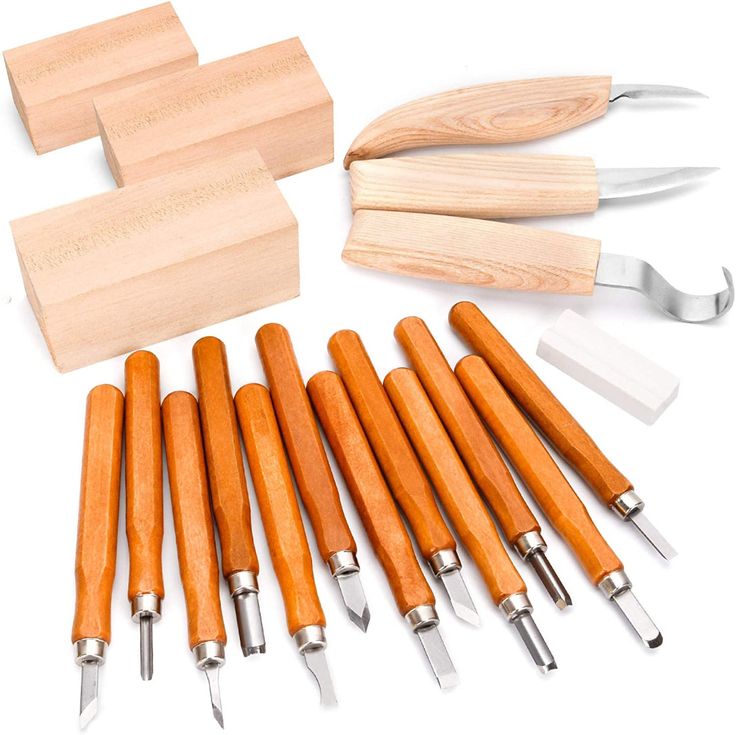
Carving animals can be fun and challenging. Learn how to make caricatures using wire and wood. Animal caricatures can be just as fun as human caricatures. However, they can communicate a story even without words. Caricatures exaggerate the realism of life. Carving caricatures can seem like a hard hobby, but it is possible for experienced carvers to use a variety of materials.
A wood board and chisels are the two main materials that you need for carving. A hammer and chisels are also required. Acrylic white paint, which can be purchased at a craft store, is the first layer. After you have completed the base layer, you can move on to the second layer. The second layer will be a mixture of golden brown paint and some burnt sienna (Academy). For the face, you should use 2 drops of sunkissed peach.
FAQ
What is the difference in plywood and particleboard?
Plywood consists of layers made from wood and pressed together by pressure. Plywood can be cut to different thicknesses. It's commonly used as flooring and cabinets. Particle board is made up of sawdust mixed in resin, then compressed into large pieces. It's used for home improvement projects. Both types of boards are durable and easy to cut.
How often do I need to buy new supplies
Some tools will need to be replaced over time. Hand tools will need to be sharpened regularly. If you are using power tools, you will need to purchase replacement parts regularly. Spread your purchases over several months to avoid purchasing too many items at once.
What material would your recommendation be to learn woodworking?
Start with softwoods such as pine and poplar. You will feel more comfortable with these softwoods, so you can move onto hardwood.
Where can I start woodworking?
Building furniture is the best way to learn how furniture is made. Although you will need to have tools and may make mistakes along your journey, you'll soon be able to master it.
Begin by choosing the project that you want to finish. It could be something as simple as a box or as elaborate as a full-scale entertainment center. Once you have chosen a project, locate a local woodworker who is skilled in this kind of work. Ask him or her for advice on what tools you'll need and where to find them. Perhaps you could ask if there is someone else who does this type of work.
What is the minimum investment a hobbyist needs to make in order to get started?
You will need capital to purchase the tools and supplies you need to start your woodworking business. A good place to start would be by buying a small table saw, drill press, circular saw, jigsaw, and sanding machine. These items aren’t too expensive so you won’t have to break the bank.
How much should a woodworker charge per hour?
The hourly rate for a professional Woodworker will vary depending on many variables, such as experience, skill level and availability.
The hourly average rate for skilled woodworkers runs between $20-$50.
A woodworker with less experience may be able to charge $10 an hour.
Statistics
- In 2014, there were just over 237,000 jobs for all woodworkers, with other wood product manufacturing employing 23 percent; wood kitchen cabinets and countertop manufacturing employing 21 percent. (theartcareerproject.com)
- If your lumber isn't as dry as you would like when you purchase it (over 22% in Glen Huey's opinion…probably over 10-15% in my opinion), then it's a good idea to let it acclimate to your workshop for a couple of weeks. (woodandshop.com)
- Woodworkers on the lower end of that spectrum, the bottom 10% to be exact, make roughly $24,000 a year, while the top 10% makes $108,000. (zippia.com)
- The best-paid 10 percent make $76,000, while the lowest-paid 10 percent make $34,000. (zippia.com)
External Links
How To
How to join two pieces of wood together without nails
Woodworking is a popular hobby. Woodworking can be a fun hobby because you can work with your hands to make useful objects from wood. However, there are times when you want to join two pieces of wood together without having to use nails. This article will explain how to do this so that your woodwork projects stay beautiful.
First, remove any sharp edges from the wood pieces before you join them. You don't want to leave sharp corners that could cause problems later on down the road. After you have completed this step, you are ready to glue your boards together.
If you're working with hardwood, you should only apply glue to one side. If you're using softwoods like pine or cedar, you should put glue on both sides. Once the glue has dried, press the boards together until they are fully adhered. After applying the glue, let dry the boards before proceeding to the next stage.
After you've glued your boards, you'll want to drill holes into the joints where you plan to insert screws. Depending on what type screw you choose, the size of these holes will depend on how big they are. If you plan to use a 1/2 inch wood screw, drill a hole at least 3/4 inches in depth.
Once you have drilled your holes you will need to drive the screws through each joint and into the backside. Avoid hitting the board's top surface. Otherwise, you could ruin the finish. Avoid hitting the screws' ends too often when driving screws. This will prevent splitting the wood's end grain.
Once your project is complete, it's time to protect it against the elements. You can either seal the entire piece of furniture or cover the top. Either way, you'll want to use a product that will last for years to come. There are many options: oil-based varnishes; polyurethane; shellac; lacquer.
These products can usually be found at any home improvement store. It is important to ensure that you purchase the correct product for the job. Also, remember that some finishes are toxic and should never be used indoors. When handling certain finishes, wear protective gear.