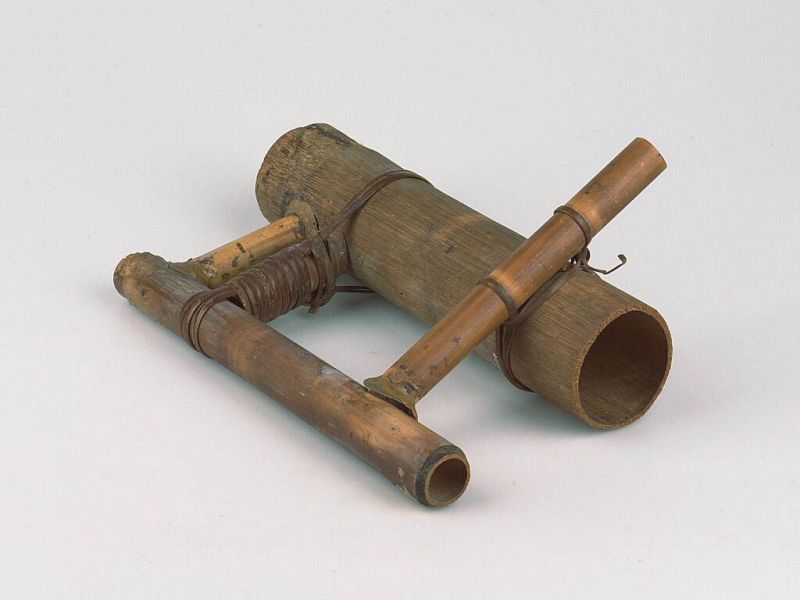
In order to support the mission of Eagle Ranch, the Chattahoochee Woodturners worked with the organization to build a woodturning studio on the school campus. The woodturners secured an Educational Opportunity Grant from the American Association of Woodturners and other donations to build the facility. Local woodturners donated tools, equipment, and other materials to help the project get off the ground. The woodturning studio is open to all students, as is a woodshop for adults with a handicap.
Hark Woodturner
Hark, a resident tutor, approached Hark eight years ago after a class. Hark accepted his offer to teach the Harvard class. After several failed attempts at teaching the course at Harvard he finally found a used lathe in the basement from a neighboring building. He began his first Harvard class that spring. Students from all Harvard Houses can now attend classes in the woodturning studio. He also continues to teach woodturning at weekends.
Arthur and Pamela, in addition to their teaching duties, have visited woodworking trade shows and symposiums in order to meet new audiences. They have hosted numerous world-renowned artists, and they have had the pleasure of hosting them. The studio has hosted a variety of woodturning workshops featuring a wide range of artists and styles. It also sent a Knight Commander and Commander to the Norwegian Woodturning Cruise every three years.
Tools
Safety gear is one of the most essential items you should have in your woodturning workspace. Safety gear can include safety goggles or eye protection to shield your eyes from the glare of sand. To keep your tools in tip-top shape, you can also invest in sharpening equipment. To sharpen your lathe blades, you will need to purchase safety gear.
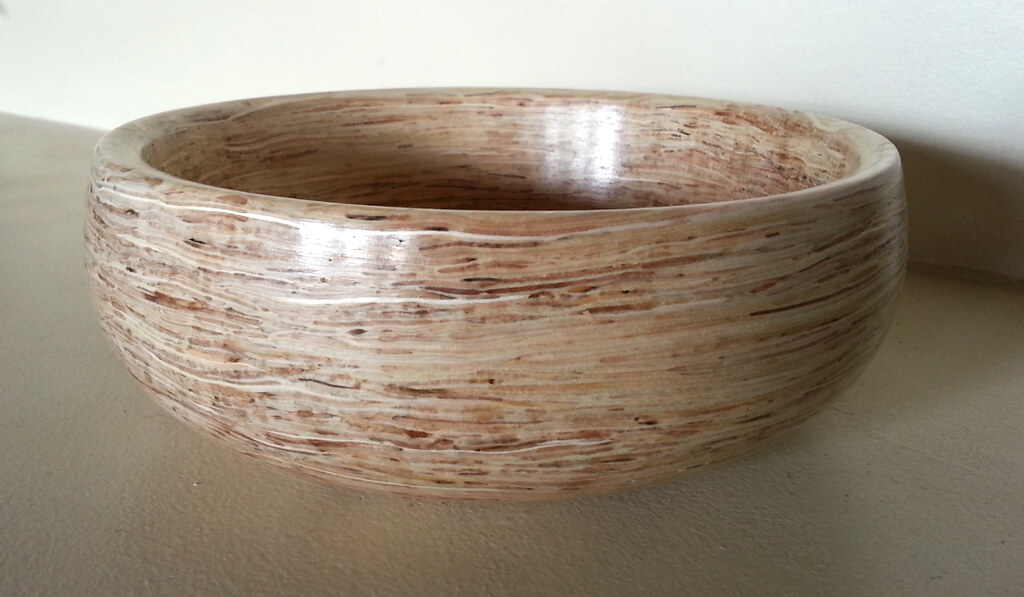
You will require a drill, a screwdriver, or a banjo as your most basic tools. The banjo allows you to slide your turning tool along the bed of the lathe, supporting the toolrest. This allows you to hold the turning tool in the most convenient location. Most modern lathes include a locking mechanism to provide added security. The banjo can be adjusted in most cases. These tools are necessary to create unique creations.
Techniques
You should be able to use the right tools and techniques whether you are woodturning for hobby purposes or as a professional. These tools are crucial for creating functional and beautiful pieces that will be both functional and attractive. These tools can be purchased online or at your local woodworking shop. The process of turning wood is time-consuming, but the results are well worth the effort.
A woodturning course is a great way of learning the basics if you're just getting started. A workshop will help you choose the best tools and techniques, as well as safety gear. A lathe will be used by participants. You will also learn how to use tools correctly and have the chance to practice different techniques as you go. Your projects can vary depending on the skills that you have, from making bowls and bottle stoppers to carving mallets.
Class size
If you are new to woodturning and are interested in learning the basics, a beginner's workshop at a woodturning studio in Durham, NC, may be perfect for you. This class will teach you basic techniques, how to sharpen tools and how to use them. You will also be involved in several projects. Safety will be stressed by the instructor. Bring a face mask or other protective equipment.
Small classes allow you to be more focused on each student's individual learning. Instructors will have ample time to answer your questions and give individual attention. Often, there will be no more than six students in a class, so you can expect to learn at a comfortable pace. Many of the classes are project-based and will take place over a couple of days. For the more advanced student, private lessons can focus on specific techniques.
Prices
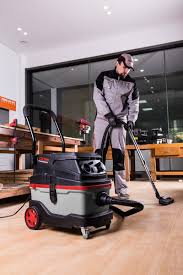
Setting up your own woodturning studio will be an expensive endeavor. Equipment and supplies can easily cost several thousand dollars. Selling your finished products at a fair price is a great way to cut down on these costs. Your profits will increase by as much as three times if you sell your finished products. You may want to sell your finished products at a lower price, even though high-end items are great ways to promote your art. While high-end items may take longer to produce, you can always sell simple items in this price range. They can even sell out in the first day of an art show that lasts two days.
A class will give you the foundations of woodturning. This will include the safe use of tools and proper sharpening. Next, you can take on more challenging projects or learn new tools and techniques. The cost for an introductory woodturning course is usually $75 for Mather residents or Harvard affiliates. All materials and tools included in the cost. A list of nearby hotels will be included.
FAQ
How can my shop be organized?
A designated place to store your tools is the first step towards keeping your workshop clean. Keep your tools away from dust and debris, so they stay sharp and ready to work. Use pegboard hooks to hang tools and accessories.
What kind of wood should I use?
There are many wood types that are used in woodworking, including oak, maple and birch. Every type of wood is different and can have a unique look and feel that will affect the final product. Oak is a darker wood and tends to be more durable than other types. Birch is lightweight and soft while mahogany is heavier and denser. You also have the option of solid wood or veneers. Veneers are thin sheets or wood that are glued together into one layer.
What is the hourly rate for a woodworker?
The hourly rate paid to a professional woodworker is dependent on many factors. These include skill level, availability, and location.
An hourly wage for skilled woodworkers is between $20 and $50.
A woodworker with less experience may be able to charge $10 an hour.
Statistics
- Woodworkers on the lower end of that spectrum, the bottom 10% to be exact, make roughly $24,000 a year, while the top 10% makes $108,000. (zippia.com)
- Most woodworkers agree that lumber moisture needs to be under 10% for building furniture. (woodandshop.com)
- If your lumber isn't as dry as you would like when you purchase it (over 22% in Glen Huey's opinion…probably over 10-15% in my opinion), then it's a good idea to let it acclimate to your workshop for a couple of weeks. (woodandshop.com)
- The best-paid 10 percent make $76,000, while the lowest-paid 10 percent make $34,000. (zippia.com)
External Links
How To
How to make wooden joints
This tutorial will teach you how to join two pieces wood together. We will use the "pockethole joint," which means that we drill holes in the wooden pieces and then glue them together. If your wood is straight and flat, this method will work well. You might consider dowel joinery if your wood isn’t straight or flat. Here are the steps
-
Drill Pocket Hole Joints. You will need to measure and mark the exact location of your pocket hole joint. With a handheld drill machine or jig saw, drill 3/4-inch deep holes in the ends of each piece.
-
Sand Smooth. The wood's edges can be sanded to prevent splitting.
-
Glue Together Apply glue to the sides of both wood. Allow it to cool for at least 5 minutes before you attach the pieces.
-
Attach the Pieces together. After the glue has dried completely, you can clamp the pieces together until they are flush.
-
Trim Joinery. Trim any excess wood surrounding the joint once the glue has dried completely.
Allow enough space between pieces so you can turn them inside out.